bearing
Our editors will review what you’ve submitted and determine whether to revise the article.
- Academia - Bearings Types
- International Journal of Research Publication and Reviews - History, Working and Application of Different Types of Bearing
- University of Arkansas Libraries - Introduction to Mechanical Design and Manufacturing - Bearings
- National Center for Biotechnology Information - PubMed Central - Design and manufacturing of roller bearing polymeric cages and development of a theoretical model for predicting the roller push-out force
bearing, in machine construction, a connector (usually a support) that permits the connected members to rotate or to move in a straight line relative to one another. Often one of the members is fixed, and the bearing acts as a support for the moving member.
Most bearings support rotating shafts against either transverse (radial) or thrust (axial) loads. To minimize friction, the contacting surfaces in a bearing may be partially or completely separated by a film of liquid (usually oil) or gas; these are sliding bearings, and the part of the shaft that turns in the bearing is the journal. The surfaces in a bearing may be separated also by balls or rollers; these are known as rolling bearings. In the illustration, the inner race turns with the shaft.
Under certain combinations of load, speed, fluid viscosity, and bearing geometry, a fluid film forms and separates the contacting surfaces in a sliding bearing; this is known as a hydrodynamic film. An oil film can also be developed with a separate pumping unit that supplies pressurized oil to the bearing; this is known as a hydrostatic film.
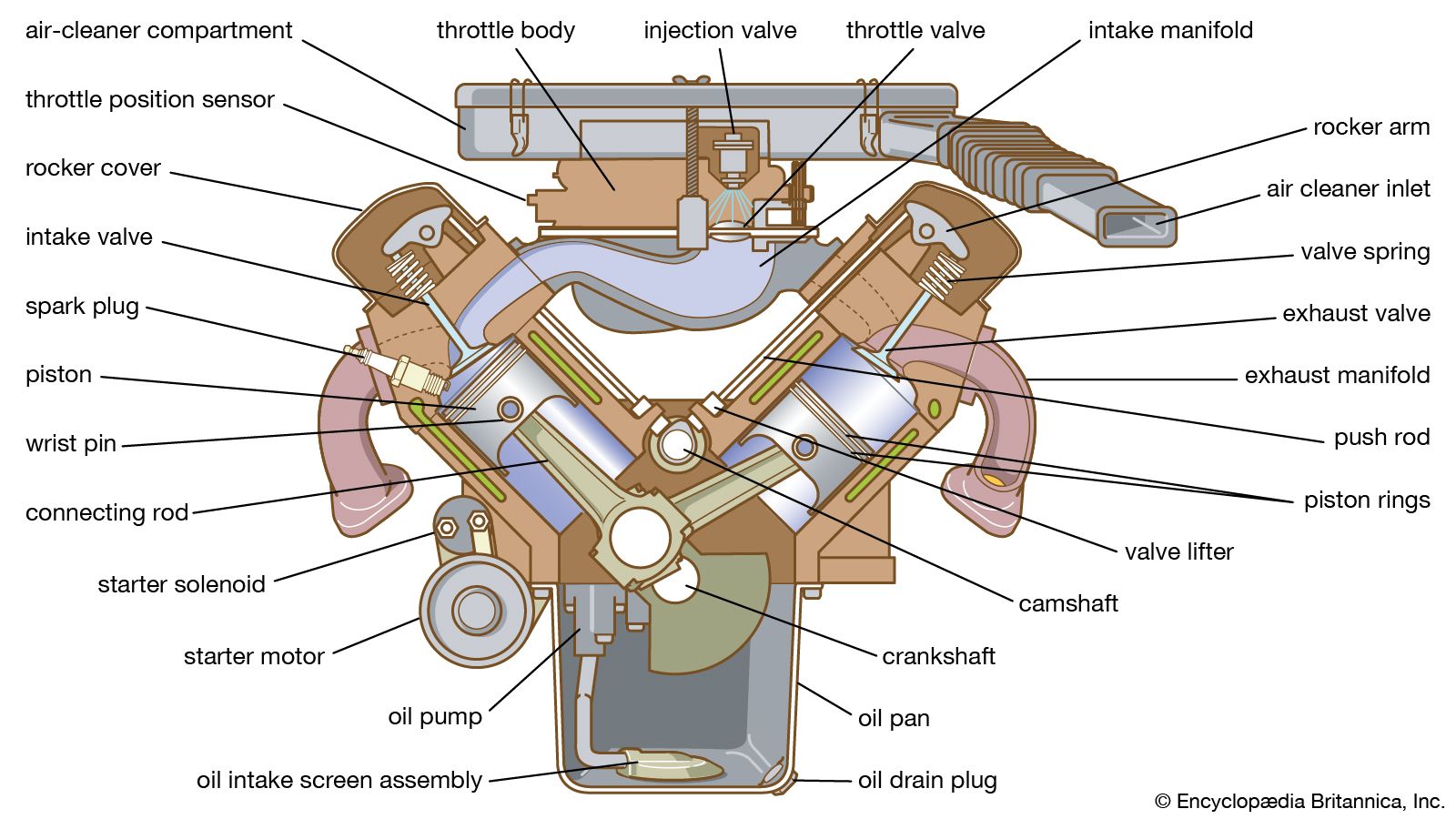
Because shaft speed is required for the development of a hydrodynamic film, the starting friction in these bearings is higher than in ball or roller bearings. To minimize friction when metal-to-metal contact occurs, low-friction-bearing materials have been developed; among these are bronze alloys and babbitt metal. See also ball bearing; roller bearing.